

Plate_Y_Offset1 = -1*(Plate_Y_Offset+Cutter_Size2)Ĭode "G1 Y-1.0 F20" ' Move cutter towards front'Ĭode "G1 Z-0.125 F15" 'Move Cutter below Stock'Ĭode "G31 Y1.5 F5" ' Move cutter towards stock'Ĭall SetDro(1, Plate_Y_Offset1) ' Set Y axis to 0 at Touch'Ĭode "G1 Y-0.50 F20" ' Move toward front'Ĭode "G1 Y0.25 F20" ' Move cutter above stock'Ĭode "G1 X-1.5 F25" ' Move cutter to left of stock'Ĭode "G1 Z-0.125 F15" ' Move cutter below stock top'Ĭode "G31 X2.0 F5" ' Move cutter towards stock, right'Ĭall SetDro(0, Plate_X_Offset1) ' Set X axis to 0 at Touch' Plate_X_Offset1 = -1*(Plate_X_Offset+Cutter_Size2) Plate_Z_Offset = Question ("What is the Touch Plate Thickness in, Ref 0.119?") 'Ref : Ĭutter_Size = Question ("What is the diameter of your cutter?") I don't use these because they ask a slew of questions before starting and it gets irritating.
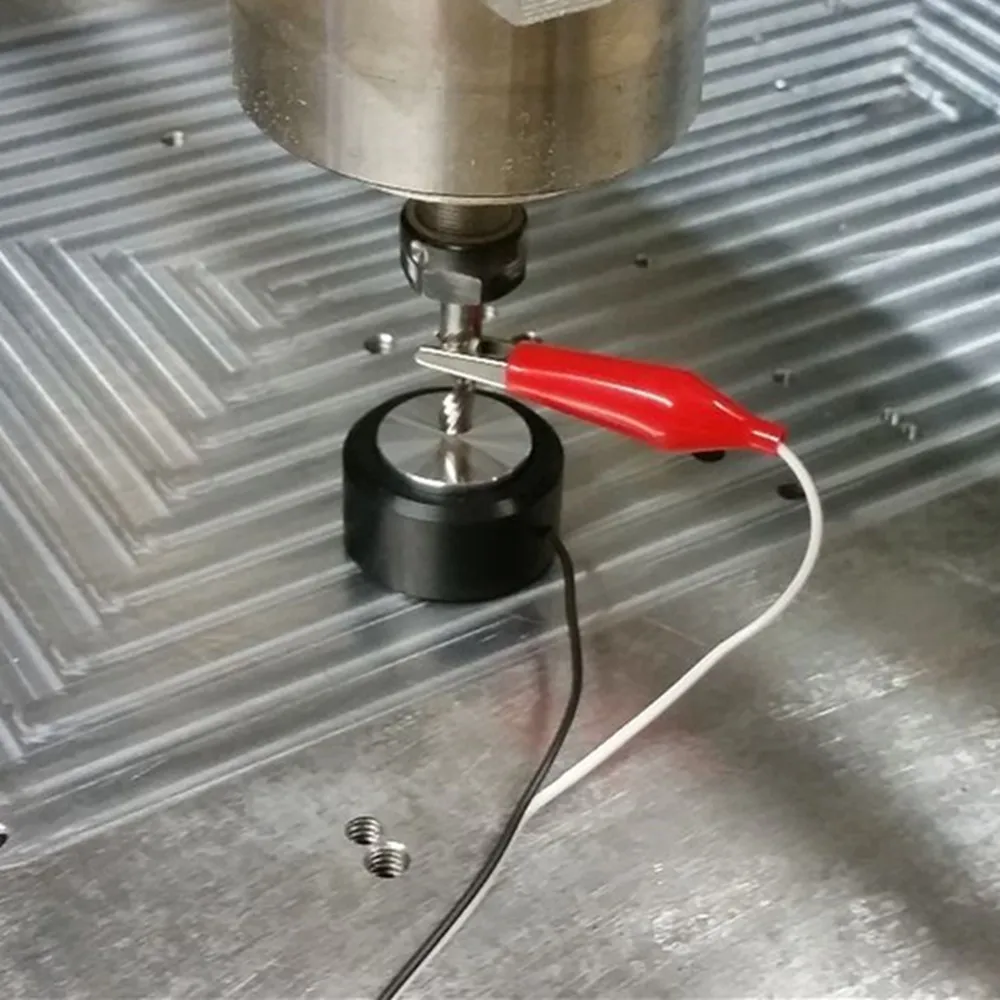
I have other codes too, they're way more complicated and I don't follow them but they allow you to use all 4 corners and edges of your work piece. Checking it will save yourself the cost of buying a new endmill MACH3 being built on Parallel ports and now stuffed into a shoddy USB protocol can cause some false positives from time to time.
#Download mach3 z axis zero touch plate code code
I should note that both this code and the next will have your tool go to X0.00 Y0.00 Z 0.500, Get a 1/2in gauge block and test it EVERY TIME to verify it works. Thanks Artsoft for not properly archiving and documenting your shit. Let me know if you do have questions, it took me about 3 months to put this together.
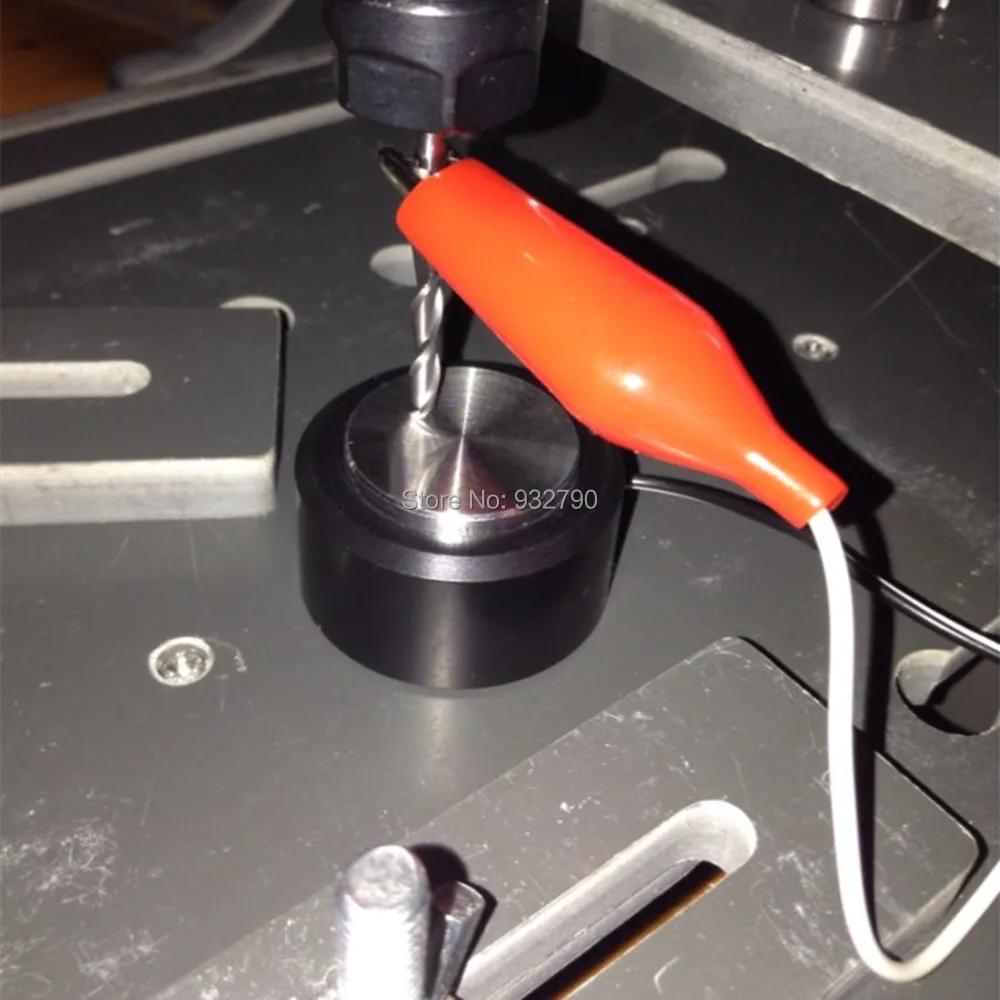
The code is in VBA for Mach so if you need explaining how that all works.good luck but it should be pretty easy to follow because I have no idea what I'm doing and I made it through. 119, you measure this as well and set it to whatever yours is. The 0.119 is the thickness of the plate itself. The offsets are the thickness of the edge of the plate, you measure this. The touch off plate I'm using is from blueOXCnc on ebay or amazon. This one is for the bottom left corner as your zero. If anyone would be able to take a look and offer some advice I would be extremely grateful.Īuto tool zero in Mach 3 is resulting in incorrect zero point even after using a number of different scripts. We are currently setting zero manually which is fine for single runs without any tool changes but eventually the machine will need to be able to cut using multiple tools and substrates which is going to require an efficient and consistent method to set the zero point My father in law lives 2.5hrs away so I am only able to work on the machine on the weekends but I have saved the script that I am hoping to use along with the XML file from Mach 3. The machine was purchased from a chinese manufacturer who has been very little help when I can actually get hold of them. I have checked all over youtube, CNCzone, Mach3 forums, etc to find the answer with little success. Also the fact that the z axis does a secondary move after it's initial retraction seems to be the cause of the error. The reason I believe this may be the case is because the issue has happened consistently with multiple scripts and even when I have adjusted the variables int eh scripts to counter the incorrect zero point it is still happening. My current theory is that I have incorrectly set something in Mach 3 which is overriding the various scripts. I know I have set my touch plate depths correctly in the scripts and I have even attempted to trick the machine by setting the tool plate to be a value less than the touch plate thickness to counter the incorrect DRO. Then it retracts again an additional 12-20mm causing the DRO to show the zero point about 20mm higher than it actually is. The tool descends as per the script, touches off on the plate and then retracts, all good so far. We have a grounding button\plate connected and I have attempted to load a number of different scripts but I am having the same issue each time I run the Auto tool zero. The build went well and everything is currently operational but I'm just having an issue with the auto tool zero function in Mach 3. The machine is running on an XHC Ethernet controller using Mach 3. I'm just chasing a bit of advice regarding a CNC I recently helped my father in law build.
